Selon que l’usine fabrique ou non sa propre pâte (usine intégrée ou non intégrée), la pâte arrive soit en suspension aqueuse directement de l’usine de pâte, soit sous forme de feuilles de pâtes séchées (pâte marchande, essentiellement de type chimique). La mise en suspension des fibres dans l’eau est la première étape de la fabrication du papier (voir shéma).
PRÉPARATION DU MÉLANGE “FIBRES-EAU
Après la mise en suspension des fibres, le mélange ‘fibres-eau’ subit en général deux opérations de préparation:
LE RAFFINAGE
Il consiste à faire passer les fibres entre les lames d’un raffineur à disques. Ce “râpage” des fibres entraîne l’apparition de fibrilles qui permettent un meilleur accrochage des fibres les unes aux autres et une meilleure homogénéité de la répartition des fibres dans la feuille de papier.
L’ÉPURATION
Avant de passer sur la machine à papier, la pâte en suspension est épurée de toute particule étrangère ou d’agglomérats de fibres. A ce stade, le mélange fibres-eau contient plus de 95% d’eau. Cette eau est essentielle pour l’étape suivante: la formation de la feuille de papier.
LA MACHINE A PAPIER
Le mélange ‘fibres-eau’ raffiné et épuré est prêt à être utilisé sur la machine à papier. Celle-ci est constituée de deux parties distinctes: la partie humide et la partie sèche.
PARTIE HUMIDE
Via une “caisse de tête”, le mélange de fibres et d’eau va être projeté de façon continue sur une toile, appelée toile de formation. Cette toile est un tissu à fines mailles, au travers desquelles l’eau va être progressivement aspirée. En quittant la toile de formation, la “feuille” de papier contient moins de 80% d’eau.
La feuille entre alors dans la section “presse” grâce à un feutre support. Cette section “presse” a pour fonction d’extraire un maximum d’eau de la feuille avant de procéder à son séchage. Au terme des opérations de pressage, le papier con tient encore environ 50% d’eau.
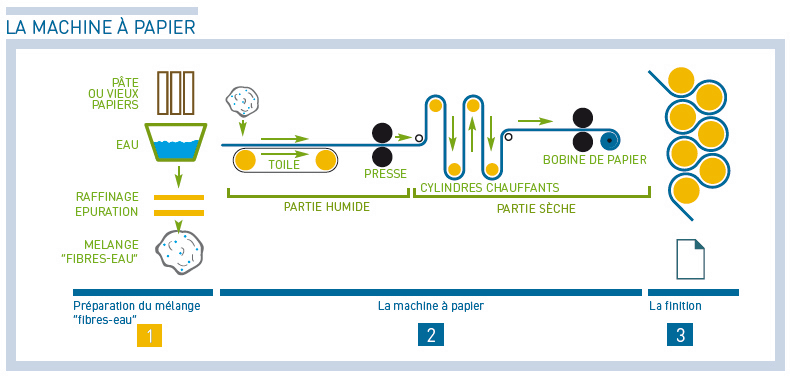
PARTIE SÈCHE
Le séchage du papier est un procédé intensif en énergie. Il peut être réalisé par:
-conduction: le papier est en contact avec un cylindre métallique chauffé à la vapeur
-convection: de l’air chaud est soufflé sur la feuille
-rayonnement: dans certains cas, des rampes à rayonnement infra-rouge augmentent la température de la feuille.
La feuille continue de papier va passer de cylindre en cylindre jusqu’à ce que son taux d’humidité avoisine 6%. Elle va alors quitter la section “sécherie” pour subir, le cas échéant, un ou plusieurs traitements de finition.
Il existe différents traitements de finition selon les types de papiers et leur destination finale. Citons ici les deux principaux.
Le calandrage consiste à faire passer le papier au sein d’une pile de plusieurs cylindres en fonte chauffés à la vapeur. Cette opération rend la surface de la feuille plus lisse et plus brillante et augmente l’imprimabilité du papier.
Le couchage consiste à recouvrir une ou les deux faces du papier avec un enduit appelé “couche” généralement composée de pigments minéraux tels que le carbonate de calcium, le talc ou le kaolin.
Cette opération vise à améliorer la surface du papier, ce qui le rendra plus performant pour une utilisation en imprimerie.
Au cours des dernières décennies, le secteur papetier a progressivement évolué vers des machines à papier toujours plus larges et toujours plus rapides. Une machine à papier moderne produit en 1 heure une feuille de 10 mètres de large et de 120km de long! Une évolution rendue possible par la mise en oeuvre de technologies de pointe.
